Alberta's Energy Transition: Recycling A Coal Mine Into Cash
Alberta is shifting. The legacy of oil, gas, and coal has begun to make way for more renewable energy. In 2023 alone, Alberta added over 500 megawatts of solar power capacity, making it the largest producer of solar energy in Canada.
With this growing focus on renewable energy, aging facilities like coal mines are being phased out, but that doesn’t mean they need to be left as relics of the past. Through mine reclamation, dismantling, and recycling, valuable materials can be recovered to generate revenue while reducing environmental impact.
Recently, Richmond Steel applied their 50 years of expertise to a decommissioned coal mine in Alberta, transforming an industrial liability into a source of cash.
How to Turn a Coal Mine Into Cash
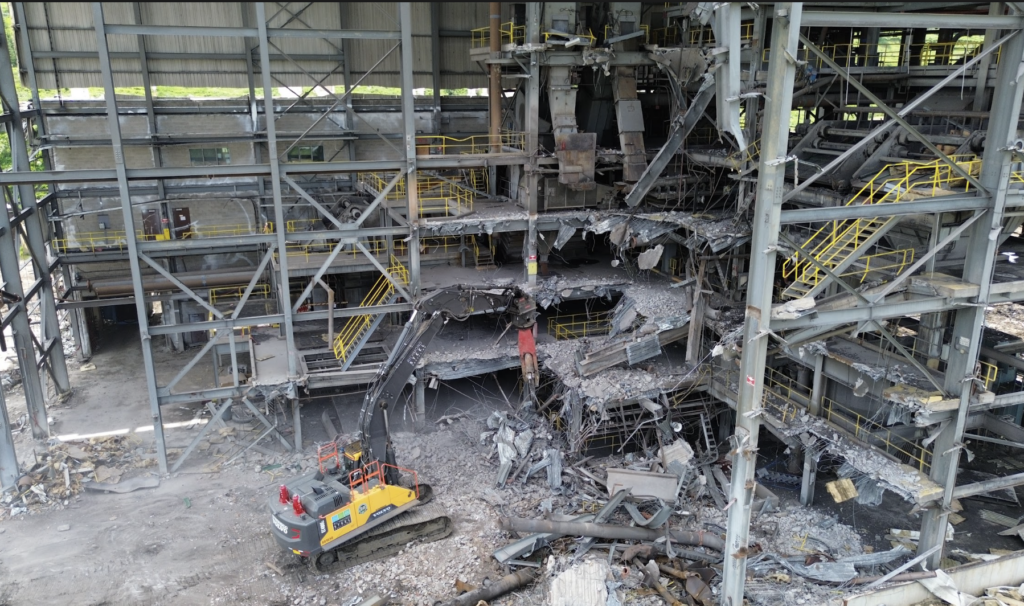
Mine reclamation isn’t just about tearing down structures; it’s a strategic process that requires careful planning, specialized equipment, and a commitment to safety and the environment.
At the Alberta site, Richmond Steel was able to recover 100% of the steel from buildings and process machinery—over 7500 metric tons. Not to mention several large transformers, motors, gearboxes, and pumps for resale.
Navigating Structural and Environmental Challenges
The mine reclamation at the Alberta site was no ordinary teardown. Richmond Steel faced multiple challenges across a large and complex site, which included three major structures: a coal wash plant, a coal dryer plant, and an electrostatic precipitator building. Additionally, two towering stacks were brought down as part of the project.
Each structure presented unique logistical, structural, and environmental hurdles that required Richmond Steel’s specialized expertise to overcome:
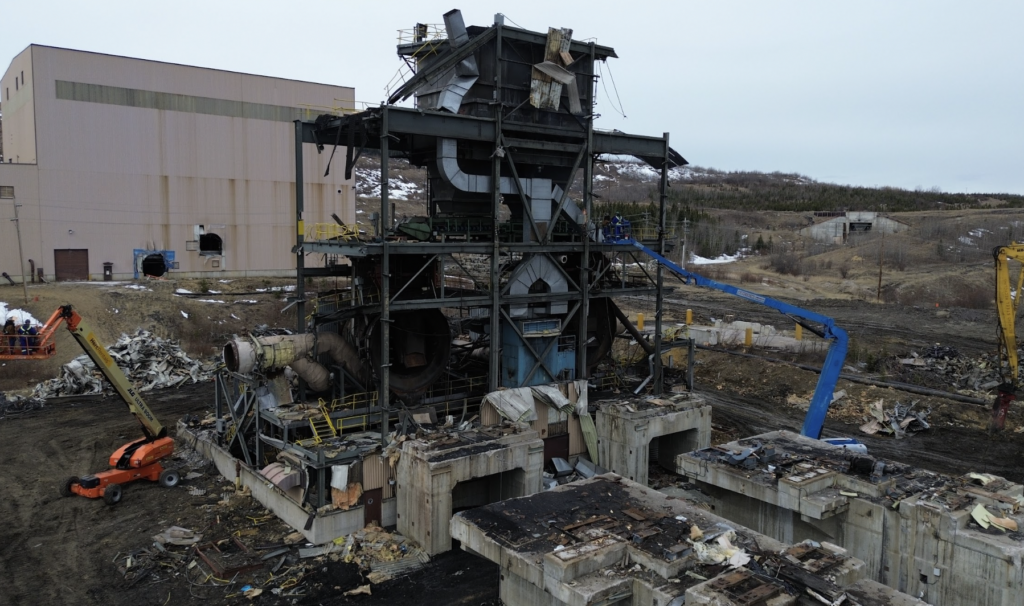
Tackling Extreme Heights
The buildings on site, some reaching 110 feet, required specialized equipment to ensure safe demolition. Richmond Steel used an ultra-high reach demolition shear, along with cables, to pull down the roof in a controlled manner.
Protecting Adjacent Structures
An admin and lab building attached to the wash plant needed to remain standing throughout the process. To ensure its integrity, Richmond Steel collaborated with a structural engineer who identified safe cut points, allowing for the wash plant’s demolition without compromising the stability of the adjacent building.
Working Around Structural Limitations
The dryer building’s basement added another layer of complexity. Due to the risk of equipment falling through the floor slab, Richmond Steel couldn’t operate machinery directly on the floor. Instead, they used a high-reach excavator from the outside, dismantling the building from the perimeter inward to safely complete the demolition.
Managing Environmental Risks
The building’s glass-fiber insulation posed a risk of spreading debris into nearby rivers and trees. Richmond Steel addressed this by placing insulation in covered waste bins immediately upon removal and installing a snow fence around the site to capture any stray material. This approach minimized the environmental impact of the project.
Safely Lowering Heavy Machinery
Richmond Steel also faced the challenge of handling large machinery located on the upper floors. Using torch cutting, the team made strategic cuts to weaken key points, then safely lowered the equipment to the ground using cables and excavators. This careful approach eliminated risk to personnel and ensured the machinery was safely recovered.
Efficient Logistics and Cleanup
Richmond Steel began by using demo grapples to remove and bale building cladding on-site, reducing transportation costs.
Large coal processing machines were safely dropped using strategic cuts and cables. They were then downsized with torch cutters and trucked to Richmond Steel’s Edmonton rail siding for direct shipment to a Seattle steel mill.
For the final cleanup, the team used large magnets, a skid steer with landscaping screens, and manual labor to prepare the site for land reclamation as part of the broader mine reclamation process
Conclusion
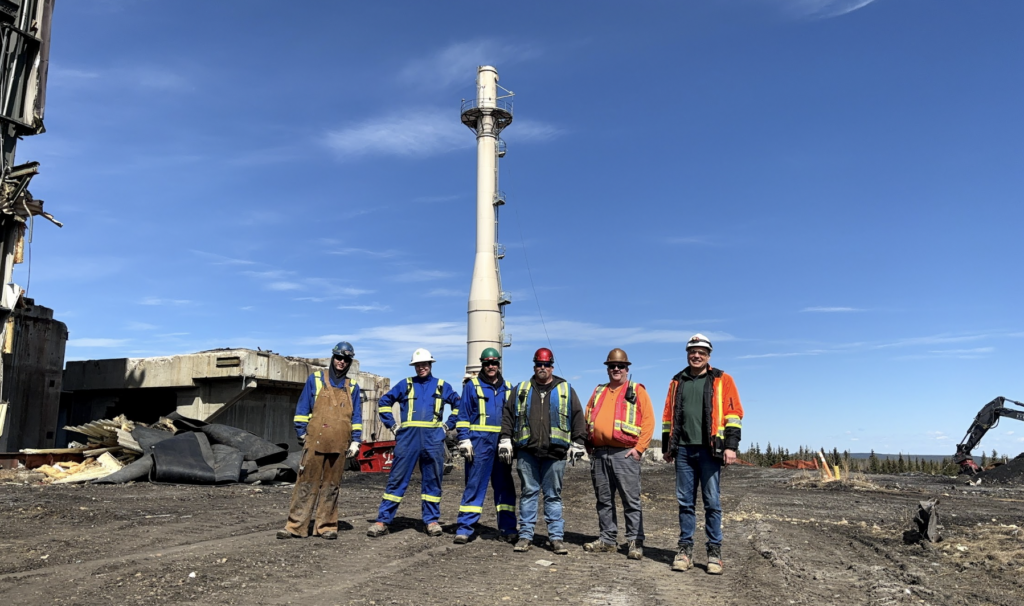
Through comprehensive mine reclamation, Richmond Steel turned a decommissioned coal mine in Alberta into profit, recovering over 7,500 metric tons of steel and valuable equipment—all while upholding safety and environmental care.
As Alberta continues to transition to renewables, Richmond Steel continues to help clients unlock value from their legacy sites.
If you have a coal mine, oil & gas site, or other facility for demolition, contact Richmond Steel to turn your assets into cash today.